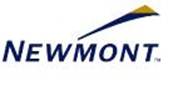 Newmont Ghana Gold Limited has Planning opportunities/jobs in Ghana to recruit Process Maintenance Foreman (Planner). We are one of five core operating regions of Newmont Mining Corporation (www.newmont.com), one of the largest gold companies in the world. Newmont operates the Ahafo Mine in the Brong-Ahafo Region and the Akyem Project in the Eastern Region. The company has approximately 46,000 employees and contractors worldwide, and employs over 6,500 employees and contractors in Ghana. JOB SUMMARY | Company: | Newmont Ghana Gold | Industry: | Mining | Category: | Engineering | Location: | Akyem | Job Status: | Full-time | Salary: | GH¢ | Education: | BSc | Experience: | 4 years | Job Expires: | 04 Jan, 2013 | PURPOSE:Perform maintenance planning and scheduling for the process plant - To prevent equipment breakdowns.
- To reduce unplanned equipment maintenance.
- To provide support to the Maintenance work groups.
- To increase reliability and availability of plant equipment.
- To plan and utilize available resources.
- To ensure that maintenance works are carried out under safe conditions.
- Interact with purchasing and stores to ensure that parts, supplies and resources are available to accomplish work assignment
- within maintenance department in a timely manner.
ESSENTIAL DUTIES: - Become familiar with and strictly adhere to Newmont's Health, Safety and Environmental standards. Act as a role model in complying with and supporting these standards and practices.
- Manage new work requests, including:
- Check for duplicate requests.
- Review request and determine if valid.
- Prioritize, set due date and obtain approvals as required.
- Convert work requests to work orders.
- Attach standard jobs where they exist.
- Manage the work request backlog.
- Fully Plan Work Orders, including:
- Review outstanding work orders with priority P3 or P4 to identify jobs to be planned.
- Identify and document planning details including but not limited to job scope, task list, procedures, resources, skill sets, parts, materials, services, job duration, cranes & hoists, special tools, required plant, outage requirement, cost estimate, safety requirement & notifications, risk assessments, permits, isolations and quality checks.
- Obtain work approval as required.
- Create reservations and requisitions for parts, materials,
- services and special tools & equipment.
- Set work order status to fully planned.
- Create MSTs with Standard Jobs.
- Update and create Standard Jobs for all repetitive corrective
- work.
- Create APLs.
- Create Work Packs.
- Organize and facilitate backlog review meetings with key
- stakeholders as required.
- Assist Maintenance Supervisors to plan and resource P1 & P2 work orders, as required.
- Schedule Work Orders and Issue Work Packs, including:
- Identify Assets available for work in the next schedule period.
- Run Forecast for the next schedule period.
- Run and distribute the following reports for each scheduling
- period to relevant stakeholders: Outstanding Work Report,
- Weekly Scheduling Report, Work Order Parts and Material
- Availability Report
- Prepare and review draft schedule with relevant stakeholders, update and finalize.
- Distribute committed schedule to stakeholders and prepare weekly schedule folders for each work group.
- Manage Completion of Work Orders in the CMMS, including
- Update Component Tracking in CMMS.
- Ensure Work Orders are completed with appropriate labor,
- materials and coding in a timely manner.
- Review closing comments and improvement suggestions on completed work orders and ensure they are actioned appropriately to improve future planning.
- Produce KPIs for each period, review performance and take action to improve.
- Plan and Schedule Shutdown work as Required, including:
- Review work orders and MSTs for inclusion in shutdowns and change work groups as required.
- Export shutdown work orders to MS Project, as required.
- Determine shutdown critical path activities, update
- shutdown schedule as required. Update CMMS based on
- changes made to the shutdown schedule.
- Finalize and commit shutdown scope, budget and schedule.
- Attend, participate and lead regular planning, scheduling and
- shutdown meetings as required.
- Contractor management including work orders, service orders, tracking purchases to ensure that preferred suppliers of labor and
- materials are used and rates adhered. Manage Invoices and
- payment approvals.
- Assist Maintenance Supervisors to plan and resource P1 & P2 work orders, as required.
- Manage coding of work orders to suit the requirements of the budgeting tool (AMT).
- Develop, with assistance from Maintenance Data Engineers, detailed job plans and discuss quality with General Foreman
- Planning and/or Senior Maintenance Planner.
- Accountable for the completion of all tasks identified in the Processing Maintenance MOS Elements to the specified quality and timeliness as assigned to this role.
The above duties and responsibilities are representative of the nature and level of work assigned and are not necessarily all-inclusive. WORKING CONDITIONS: Position is located in a very remote location. The physical demands and work environment characteristics described here are representatives of those that must be met by an employee to successfully perform essential functions of this job. - Specific vision abilities required by the job include close vision, distance vision, color vision, peripheral vision, and ability to adjust
- focus.
- Physical Demands: While performing the duties of the job, the employee is required to sit at a desk for extended periods, climb stairs, walk and stand.
- Work Environment: The noise level in the office work environment is minimal. Occasional exposure to noise, fumes, high temperature
- hazardous materials, sharp edges, dust, pinch-points, vibration,
- slippery surfaces etc.
Required Skills or Experience ESSENTIALS SKILLS AND EXPERIENCE: - Degree in Mechanical or Electrical Engineering or HND Mechanical or Electrical Engineering with minimum 4 years working experience in the process plant.
- Be strong team player.
- Commitment to company values.
- Thorough knowledge of maintenance principles and industry standards.
- Thorough knowledge of the work management process.
- Thorough knowledge of planning and scheduling.
- General knowledge of performance measures and their interpretation.
- General knowledge of defect elimination methodologies and their interpretation.
- Thorough knowledge of the operation of the CMMS (Ellipse/SAP).
- Ability to effectively prioritize jobs in order of importance
- Strong knowledge in MS Office Suite and MS Project.
- Ability to interpret mechanical and electrical engineering drawings
DESIREABLE SKILLS AND EXPERIENCE: - Training and experience in Condition-Based Maintenance (CBM) techniques, such as Vibration Analysis, Thermography and Oil Analysis.
- Knowledge and experience with Reliability Centered Maintenance (RCM), Root Cause Analysis (RCA), Top 10 Analysis of Breakdowns.
Interested applicants should please create a profile and apply at the Newmont's website at www.Newmont.com/Join-Our-Team This is the preferred mode of application. However, if you do not have access to an Internet resource, please send your CV and cover letter to the site HR office before or on the closing date. The HR Manager Newmont Ghana Gold Limited PMB Airport Post Office Accra, Ghana Search for Other Jobs Here |
0 comments:
Post a Comment